How can I avoid the tool breaking inside the tool bushing?
The primary reason the tool breaks inside the bushing is insufficient greasing. In light applications, greasing should be carried out in accordance with the manual, assuming that the hammer isn’t equipped with an automatic lubrication system. In more demanding applications such as tunneling and trenching or the demolition of reinforced concrete, greasing has to be done more frequently, as often as every 30 minutes in some applications.
In the event of a hammer malfunction, what can I do to avoid high repair costs?
In the event of a catastrophic hammer malfunction, stop the hammer immediately to isolate the cause. If you find an oil leak, check the hose connectors first. If this is not the cause of the leak, take the hammer to your local dealer for servicing. Also, be sure to check the tool bushing condition regularly, if you can insert a pencil between the tool and the bushing, the bushing needs to be replaced – You might save the piston.
Why do short impact cycles reduce operating costs?
Long impact cycles of more than 20 seconds can cause the impact head of the piston to heat up, causing damage or “mushrooming”. The piston might also start to vibrate inside the cylinder, breaking the lubricating oil film and causing seizure between the piston and cylinder. In addition, the tool tip can heat up, causing more rapid wear. In extreme cases where the tool begins to glow red, it could become worn out in a single day!
What can I do to the excavator to reduce operating costs?
The most important thing is ensuring the correct flow and free return line. Overflow will always reduce the lifetime of hammer. Do not install the hammer on a new excavator without first checking the flow. If your excavator has a hammer mode, make sure the programming is correct for your hammer and that your operator remembers to use the hammer mode. On large hammers, the return flow should always go directly to return filters. For more information consult your local hammer dealer.
Does periodical maintenance actually reduce operating costs; maintenance is also a cost?
During periodical maintenance, the seals and membrane will be replaced. There is also an inspection of all the parts, with wear items being replaced as necessary. By doing periodical maintenance regularly, you might be able to avoid major, unplanned breakdowns, ensuring that your hammer achieves the highest possible levels of availability and profitability.
Does the application influence operating costs?
Yes it does. Inspections and maintenance periods will be shorter in certain applications. For further information, please contact your local hammer dealer.
What else can I do to reduce operating costs?
One of the biggest factors that will dictate the owning and operating costs and overall profitability of a hydraulic hammer is the skill and competence of the operator. Ask your dealer if they can arrange some operator training and ensure that your operators adhere to the operating and maintenance procedures detailed in the owner’s manual.
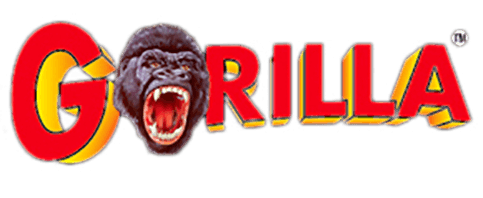